Drying Processes
Speeding up offset, digital, inkjet drying processes
General Information
For high speed printing processes, the limiting factor on the productivity of the equipment is usually ink drying time. To maximize printing speed without quality loss, it is important to be able to determine quickly when the printed substrate is sufficiently dry or fused.
The surface temperature of a “wet” substrate will change (rise) very slowly as constant heat is applied to the product. This occurs because the moisture in the substrate absorbs much of the heat energy as it evaporates.
At the point that the substrate becomes ‘dry’, however, the same constant heat supply will quickly raise the temperature until it reaches the same as the surrounding air.
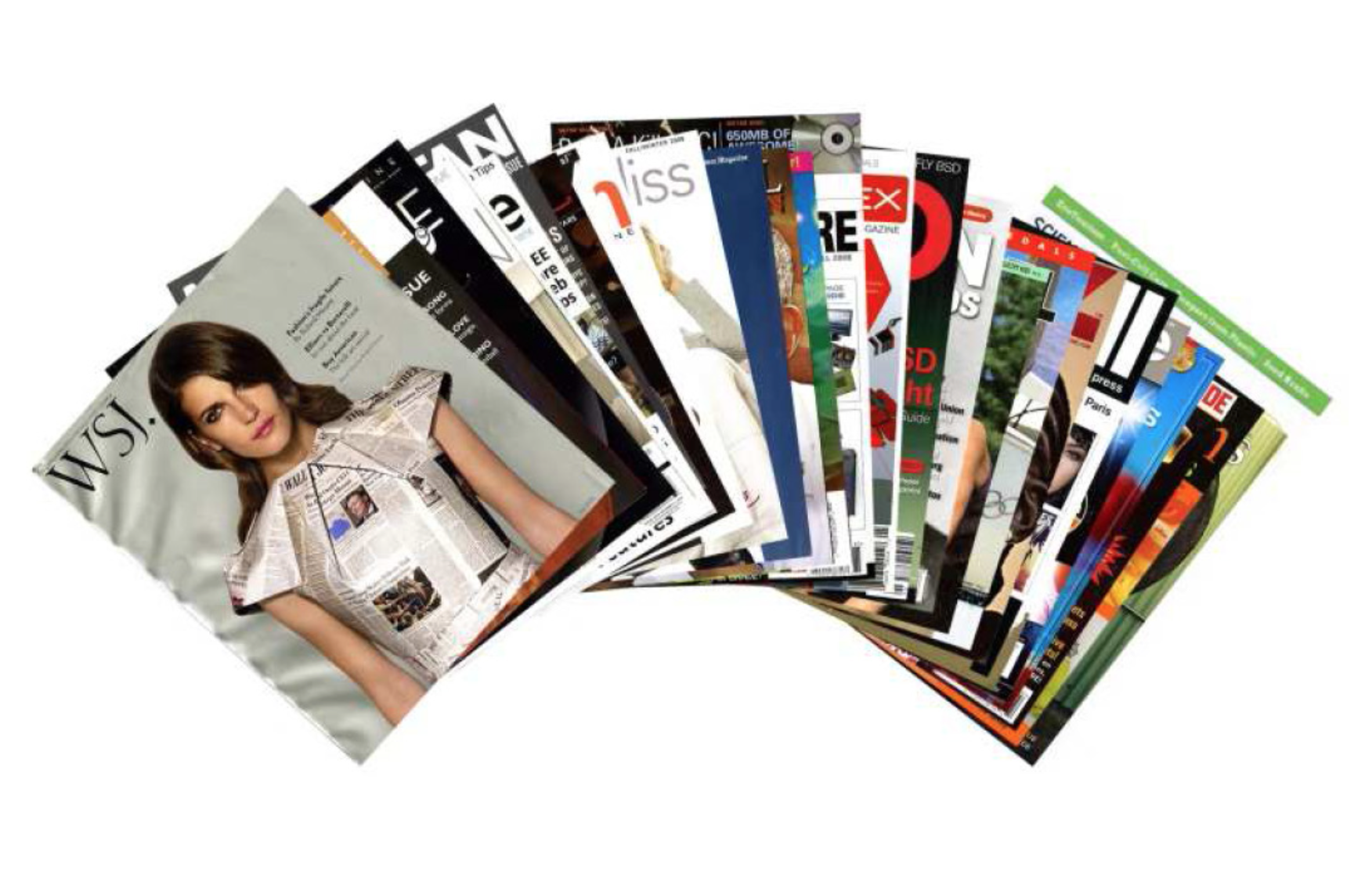
The Optimal Solution
Infrared temperature sensors will allow for fast measurement and no contact with the product.
With the response time of the IRt/cs averaging around 100 milliseconds, you can quickly detect the dry out point and increase your production speed and yield.
You can also find the ‘dry out’ point by installing an array of lRt/cs, and with the side view mounted sensors you can reach hard to access areas on any web process.
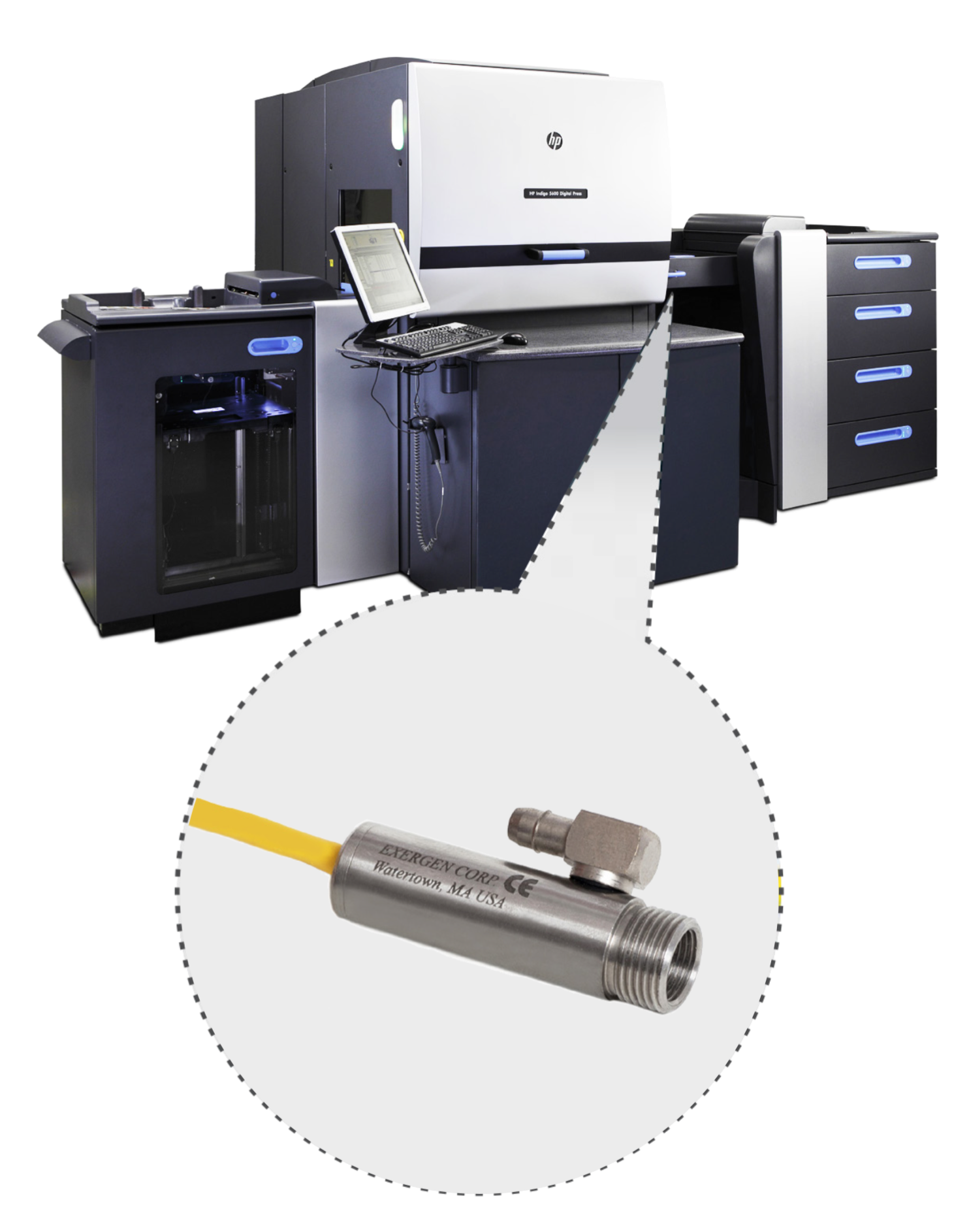
Why Exergen IR Non-Contact Sensors?
- IRt/cs are self powered and intrinsically safe
- Repeatability error of 0,01°C (0.02°F)
- Interchangeability error ± 1%
- Resolution of approx. 0,0001°C (0.0002°F)
- Side view sensors if the available space is limited
- All sensors are CE and RoHS rated
Commercial Advantages
- Increase
- production by increasing the printing speed
- quality of the end product
- yield
- profit